Please select your location and preferred language where available.
Fluorine-free Word Line Molybdenum Process for Enhancing Scalability and Reliability in 3D Flash Memory
September 24, 2024
To achieve both higher bit density and lower cost in 3D flash memory, it is essential to increase the number of stacked word lines (WLs) while simultaneously scaling horizontally (XY dimensions) and vertically (Z dimension). Z scaling (WL pitch scaling), however, degrades WL resistance and worsens parasitic RC delay. Shrinking the XY dimensions involves reducing the pitch between memory holes (MH pitch) and increasing the number of MHs in a row. These scaling approaches make the embedding of tungsten (W) WLs more difficult. They increase voids and slits in W WLs that then act as a source of leftover fluorine (F) atoms originating in the precursor, WF6. These F atoms can attack cell dielectrics and inter-WL dielectric, causing leakage failures[1][2][3]. These performance and reliability degradations are among the most critical scaling limiters for 3D flash memory.
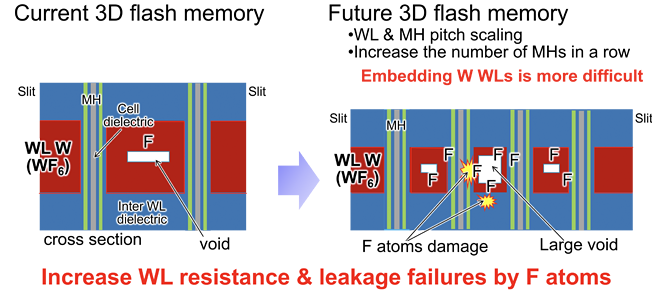
Molybdenum (Mo) is a suitable alternative to overcome these scaling limits. Mo, as a physical property, has lower resistivity than W and its precursor, MoO2Cl2, is free of F atoms. We present the advantages of the state-of-the-art fluorine-free WL Mo process over the WL W process in 3D flash memory[4].
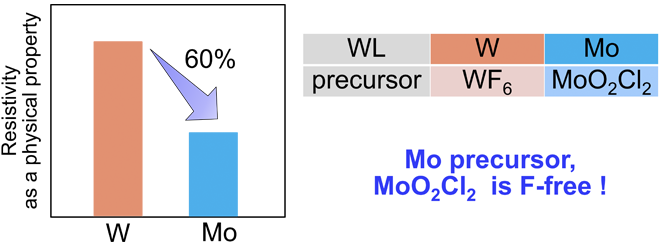
We have demonstrated that embeddability is as important in the WL Mo process as in the WL W process. Figure 3 shows the relationship between embeddability and leakage failure rate. It can be seen that the higher the embeddability, the lower the leakage failure rate. Figure 4 shows the relationship between embeddability and oxygen intensity in the WL Mo film analyzed by time-of-flight secondary ion mass spectrometry (TOF-SIMS). It can be seen that as embeddability increases, oxygen intensity decreases. The Transmission Electron Microscopy Energy Dispersive X-Ray Spectroscopy (TEM-EDX) image shown on the left side of Figure 4 confirms that oxygen accumulates in voids in WL Mo. As the embeddability becomes worse, the voids, containing residual oxygen due to the precursor MoO2Cl2, become larger. When the residual oxygen atoms in these voids diffuse into the cell dielectrics and inter-WL dielectric, they form leakage current paths leading to leakage failure. Therefore, it is important to improve embeddability in the WL Mo process.
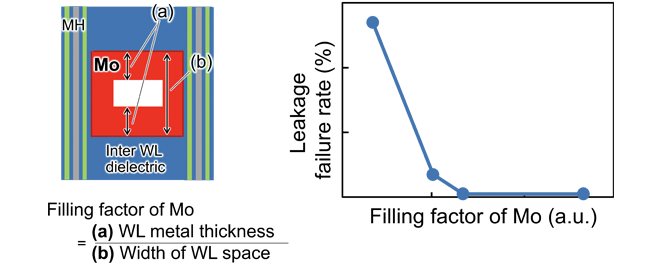
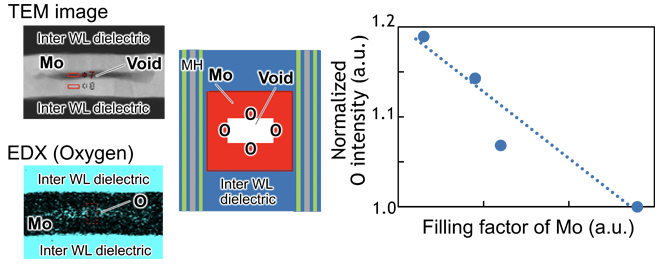
Figure 5 compares the leakage failure rate of WL Mo with improved embeddability and WL W. It can be seen that WL Mo has a leakage failure rate that is 1/100th that of WL W. The fluorine-free WL Mo process has demonstrated that it can significantly reduce leakage defects by eliminating fluorine damage, which is a problem in the WL W process.

Figure 6 shows the WL RC of WL Mo and WL W when scaling the WL pitch (scaling in the Z dimension). The WL RC of WL Mo is better than WL W at any pitch, with an 18% improvement when the WL pitch is reduced by 17%. This is due to the lower resistivity of Mo compared to W as a material. This result confirms that WL Mo can shrink WL pitch by more than 7.3% even when the given RC is same as WL W.
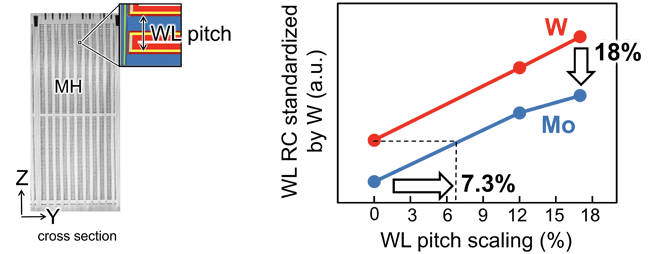
Figure 7 shows the leakage failure rates of WL Mo and WL W when scaling the MH pitch (scaling in the XY dimension). For WL Mo, unlike WL W, the increase in leakage failure rate when scaling the MH pitch is minute. When the MH pitch is reduced by 3.7%, the leakage failure rate of Mo WL reaches 1/25th that of W WL. It is sufficiently low compared to the leakage failure rate of WL W without scaling. This result confirms that WL Mo can shrink MH pitch by more than 3.7%.
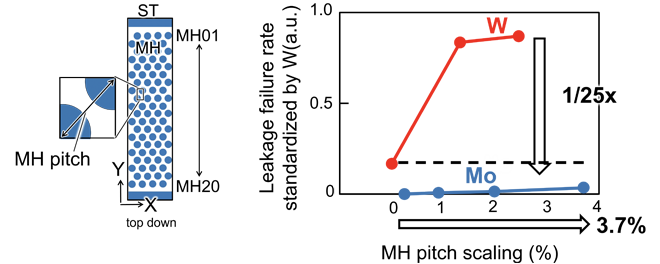
From these results, Mo WL can realize more than 16.3% increase in bit density in the same Si die volume by XY and Z dimension scaling.
The advantages of the state-of-the-art fluorine-free word line Mo process for 3D flash memory have been demonstrated. The optimized Mo filling can dramatically improve cell reliability by reducing damage to cell dielectrics and inter-WL dielectrics during XYZ scaling. These techniques enable us to extend the scaling limit of 3D flash memory.
These results were presented at the international conference 2024 Symposium on VLSI Technology and Circuits held in June 2024[4], based on joint development with Western Digital Corporation.
Reference
[1] Yu-jie Song et al., “Modeling and Optimization of Array Leakage in 3D NAND Flash Memory”, 2018 IEEE International Conference on Integrated Circuits, Technologies and Applications (ICTA), 2018, pp.120-121
[2] Tuung Luoh et al., “Tungsten Gate Replacement Process Optimization in 3D NAND Memory”, 2019 Joint International Symposium on e-Manufacturing and Design Collaboration (eMDC) & Semiconductor Manufacturing (ISSM), 2019, pp.1-4
[3] Soochan Chung et al., “Process Improvements for 7th Generation 1Tb Quad-Level Cell 3D NAND Flash Memory in Mass Production”, 2023 IEEE International Memory Workshop (IMW), 2023, pp.17-20
[4] Takashi Fukushima et al., “Fluorine-free Word Line Molybdenum Process for Highly-Scalable and Highly-Reliable 3D Flash Memory”, 2024 IEEE Symposium on VLSI Technology and Circuits, 2024, T6-1.